¿Qué sistema de escaneo es adecuado para soldar horquillas de cobre en motores eléctricos?
Tecnología de horquilla
La eficiencia del motor de accionamiento EV es la misma que la eficiencia de combustible del motor de combustión interna y es el indicador más importante directamente relacionado con el rendimiento. Por lo tanto, los fabricantes de EV están tratando de aumentar la eficiencia del motor al reducir la pérdida de cobre, que es la mayor pérdida del motor. Entre ellos, el método más eficiente es aumentar el factor de carga del devanado del estator. Por esta razón, el método de devanado de horquilla se aplica rápidamente a la industria.
Horquillas en un estator
El factor de llenado de ranura eléctrica de los estatores de horquilla es de alrededor del 73% debido al área de sección transversal rectangular de las horquillas y al menor número de devanados. Esto es significativamente más alto que con los métodos convencionales, que logran aprox. 50%.
En la técnica de horquilla, una pistola de aire comprimida dispara rectángulos de alambre de cobre (similar a las horquillas) en ranuras en el borde del motor. Para cada estator, entre 160 y 220 horquillas deben procesarse en no más de 60 a 120 segundos. Después de esto, los cables están entrelazados y soldados. Se requiere una precisión extrema para preservar la conductividad eléctrica de las horquillas.
Los escáneres láser a menudo se usan antes de este paso de procesamiento. Por ejemplo, las horquillas de alambre de cobre particularmente conductores eléctricos y térmicamente a menudo se despojan de la capa de recubrimiento y se limpian por haz láser. Esto produce un compuesto de cobre puro sin ninguna influencia interferente de partículas extrañas, que pueden resistir fácilmente voltajes de 800 V. Sin embargo, el cobre como material, a pesar de sus muchos beneficios para la electromobilidad, también presenta algunos inconvenientes.
Sistema de soldadura de horquilla de Carmanhaas: CHS30
Con sus elementos ópticos potentes y de alta calidad y nuestro software de soldadura personalizado, el sistema de soldadura de horquilla Carmanhaas está disponible para el láser multimodo de 6kW y el láser de anillo de 8kW, el área de trabajo podría ser de 180*180 mm. También se pueden proporcionar tareas fácilmente procesas que requieren sensor de monitoreo a pedido. Soldadura inmediatamente después de tomar fotos, sin mecanismo de servo de movimiento, bajo ciclo de producción.

Sistema de cámara CCD
• Equipada con una cámara industrial de alta resolución de 6 millones de píxeles, la instalación coaxial, puede eliminar los errores causados por la instalación inclinada, la precisión puede alcanzar 0.02 mm;
• Se puede combinar con diferentes marcas, diferentes cámaras de resolución, diferentes sistemas de galvanómetro y diferentes fuentes de luz, con un alto grado de flexibilidad;
• El software llama directamente a la API del programa de control del láser, reduciendo el tiempo para comunicarse con el láser y mejorar la eficiencia del sistema;
• Se puede monitorear la brecha de sujeción de pines y la desviación del ángulo, y el procedimiento de soldadura correspondiente se puede solicitar automáticamente para el pasador de desviación;
• Los pasadores con desviación excesiva se pueden omitir y la soldadura de reparación se puede llevar a cabo después del ajuste final.
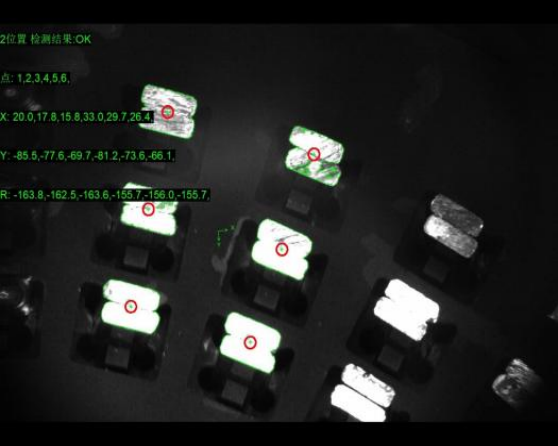
Ventajas de Carmanhaas de la soldadura del estator de horquilla
1. Para la industria de soldadura por láser del estator de horquilla, Carman Haas puede proporcionar una solución única;
2. El sistema de control de soldadura autodesarrollado puede proporcionar diferentes modelos de láseres en el mercado para facilitar las actualizaciones y transformaciones posteriores de los clientes;
3. Para la industria de soldadura por láser del estator, hemos establecido un equipo dedicado de I + D con una rica experiencia en producción en masa.
Tiempo de publicación: 24-2022 de febrero